ALLEN TWP., Pa. - A key player in the cement industry with deep roots in our region is relocating a manufacturing line to the Lehigh Valley.
FLSmidth Cement is in the process of outfitting a 122,000-square-foot warehouse it’s renting in Allen Township, Northampton County, with the machinery needed to turn it into a manufacturing, assembly, and distribution center.
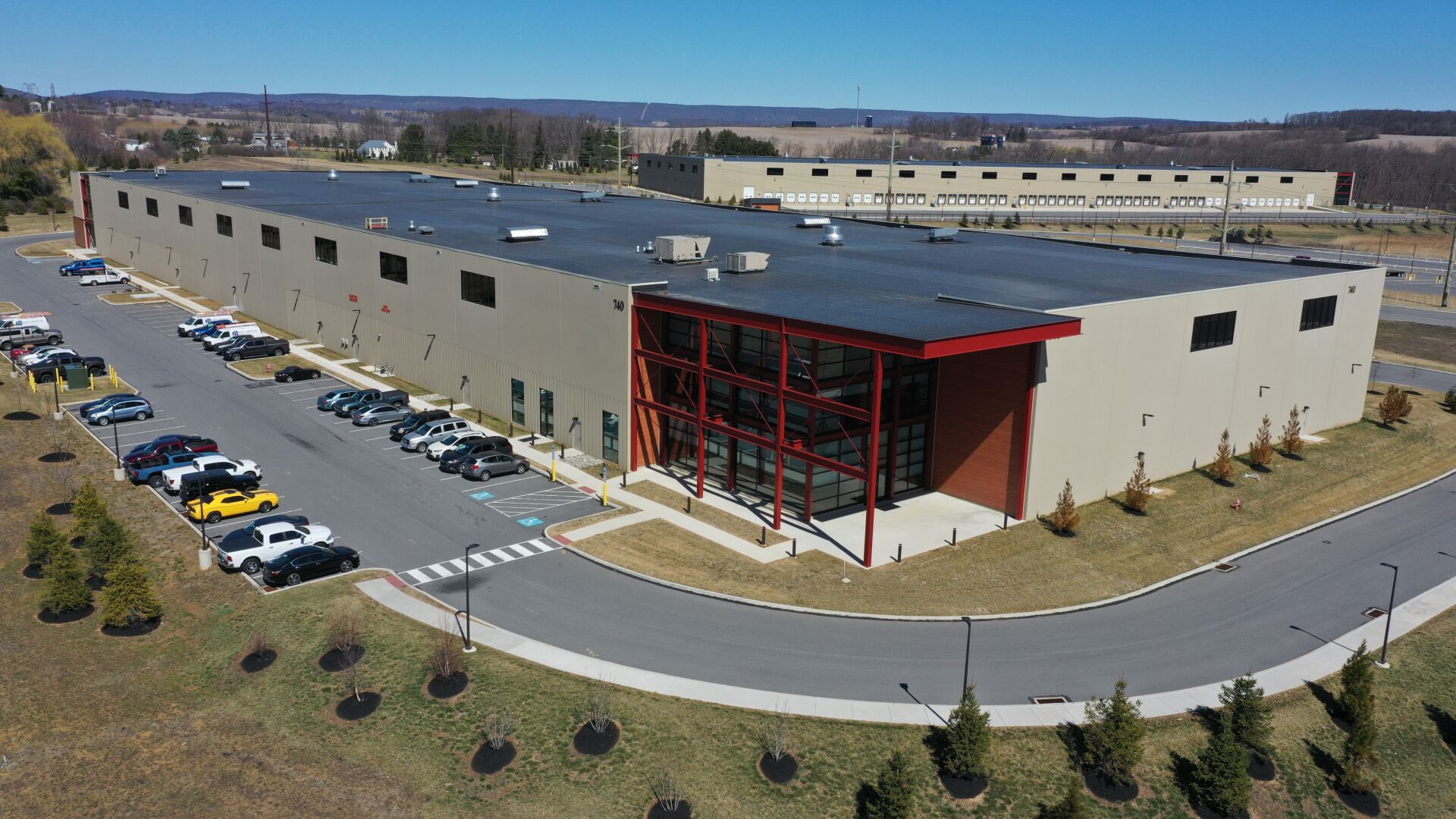
Site of new FLSmidth warehouse in Allen Twp.
FLSmidth will use the facility to make equipment for its pneumatic transfer line, which moves product - like cement - using air.
Deep Lehigh Valley roots
FLSmidth’s history in the Lehigh Valley begins more than 100 years ago, although the FLSmidth name wouldn’t officially enter the picture until several decades after that.
It was around 1918 that a man named Alonzo Kinyon (some sources say he was from Allentown, others give different birthplaces) developed a pump as a better, safer way to move pulverized coal. He was said to have been inspired by an enclosed pump he saw at a steel plant in Ashtabula, Ohio.
Kinyon’s system moved the powder through a pipeline with air. He sold his invention to the Fuller-Lehigh Company of Catasauqua. According to the Historic Catasauqua Preservation Association, company owner James Fuller III kept the rights to the invention when he sold Fuller-Lehigh and founded a new business, the Fuller Company, in 1926.
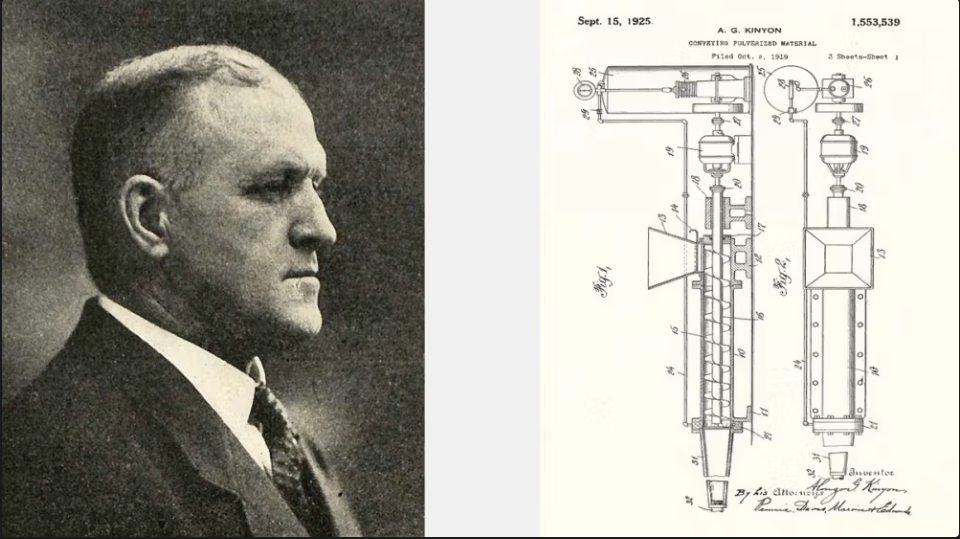
Alonzo Kinyon and the early Fuller-Kinyon pump.
The Fuller Company relocated to the former Crane Iron Works site in Catasauqua, and the Fuller-Kinyon pump, as it came to be known, became standard equipment in cement factories around the globe.
FLSmidth was founded in Copenhagen, Denmark in 1882. Initially it focused on small machinery but, by 1887, the company was building its first cement plant in Sweden.
FLSmidth acquired Fuller in 1990, and later closed the Catasauqua plant in 2004. Operations continued for a time at a separate plant on S. 10th Street in Allentown.
In 2022, the company moved its corporate office from 2040 Avenue C in Bethlehem (now the current home of Lehigh Valley Academy Regional Charter School), to Patriot American Park outside Allentown in Hanover Township. The building, formerly Agere’s global headquarters, is known as the “Emerald Palace” because of its green tinted glass.
FLSmidth also makes equipment and machinery used in the mining industry.
What's pneumatic transfer?
How exactly does pneumatic transfer work? If you’ve ever gone through the drive-through line at the bank where you had to put your documents in a little cylinder that was then whisked away in a tube, you’ve experienced pneumatic transfer. “Pneumatic conveying is pushing something through a pipeline with air,” said Fred Wuertele, who worked in sales and product management for many years for FLSmidth, and is now in an advisory role.
Of course, the process is happening on a much larger scale at a cement mill than at your local bank branch. Material is moved in bulk at many hundreds of tons an hour. Pipelines can range from just a few inches in diameter to up to two feet. “The advantage of pneumatic conveying is that the material is completely enclosed so no dust escapes," Wuertele said. "It’s very environmentally friendly compared to belt conveyors. It’s also much easier to run a pipe through a manufacturing plant than a belt conveyor. You can snake it through almost anywhere.”
The Fuller-Kinyon pump, and the Ful-Vane air compressor that works with it, which was developed in 1929, were manufactured at FLSmidth’s plant in Manheim, Lancaster County, until 2022. “Manheim was the oldest plant that FLSmidth owned and it was in need of heavy investment in order to bring it back up to the company’s standards,” Wuertele said. Rather than spring for the upgrades, FLSmidth closed the Manheim plant, and moved production of the pneumatic transfer line to facilities in Pekin, Illinois, and Tucson, Arizona.
When Wuertele was asked why manufacturing was being moved back to Pennsylvania, he said the reason was twofold. Firstly, FLSmidth is looking to divest its cement business to focus on its interests in the mining industry. “Within the next six months to a year I expect we’ll have a new owner,” Wuertele said. The plants in Pekin and Tucson are owned by the mining side.
Secondly, the company found splitting up the manufacturing line just wasn’t good for business. “Having production at two separate plants didn’t work out as well as FLSmidth planned,” said Wuertele. “Even if the company had not split, we would probably be talking about moving it back just for efficiency standards.”
Getting ready to roll
The new manufacturing site at 740 Cesanek Road in Allen Township will have about 50 people on the payroll, but that number is expected to grow over the next couple of years.
It will be FLSmidth’s fourth Lehigh Valley address at the moment. Besides the office at Patriot American Park, there’s also a small manufacturing site in Whitehall that makes carbon fiber blades, as well as a testing center in Catasauqua, where FLSmidth experiments with various materials that companies want to convey pneumatically.
An opening celebration for the Allen Township site is planned for next month, although the plant probably won’t be fully operational until the end of the year.
It will be the only place that makes the products needed for FLSmidth’s pneumatic transfer line: Fuller-Kinyon pumps, Ful-Vane compressors, feeders and air locks, and valves that can divert materials in various directions in the pipeline. “Almost every plant in the Lehigh Valley that manufacturers cement will have our product in it,” Wuertele said.
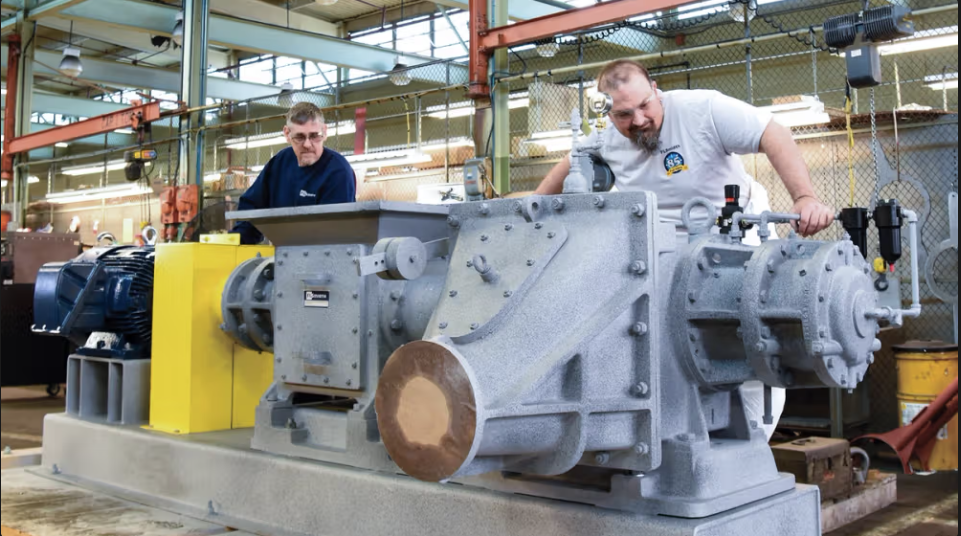
The Fuller-Kinyon screw pump today.
Some of the machines will be brand new, like a precision grinder being shipped from Italy, and a horizontal boring mill that just arrived from Japan. Others are being repurposed from the Manheim plant, including a 1935 slotter machine that makes rotors for the compressors. “It’s a super heavy-duty machine that would be very expensive to duplicate today,” Wuertele said.
The newer machines are computer controlled, but some of the older ones were “purpose built” and are still going strong, said Wuertele. “It’s a very neat mix for us manufacturing geeks.”